When planning to use MgO boards for your construction project, it's important to understand the various costs involved. Here’s a breakdown of the key components that influence the overall cost of installing MgO boards:
1. Material Costs: The price of MgO boards themselves can vary depending on their thickness, size, and quality. High-quality MgO boards with enhanced features such as better fire resistance and moisture resistance will generally be more expensive. On average, the cost of MgO boards ranges from $2 to $5 per square foot.
2. Labor Costs: Installing MgO boards requires skilled labor due to their heavier weight and harder composition compared to traditional drywall. The cost of labor can vary depending on the region and the complexity of the installation. Labor costs typically range from $3 to $8 per square foot.
3. Tools and Equipment: Special tools such as carbide-tipped saw blades and stainless steel screws are required for cutting and fastening MgO boards. If these tools are not already available, there may be additional costs for purchasing or renting them.
4. Site Preparation: Proper site preparation is crucial for a successful installation. This may include leveling surfaces, adding support structures, and ensuring the substrate is suitable for MgO board installation. The cost for site preparation can vary widely depending on the condition of the site.
5. Finishing Costs: After installing MgO boards, additional work is often required to finish the surfaces. This can include taping, mudding, sanding, and painting. High-quality finishing materials and skilled labor can add $1 to $2 per square foot to the overall cost.
6. Transportation and Handling: Transporting MgO boards to the construction site can be more expensive than lighter materials due to their weight. Handling these heavy panels on-site may also require additional manpower or equipment, adding to the overall cost.
7. Permits and Inspections: Depending on local regulations, obtaining permits and undergoing inspections may be necessary. These can incur additional costs but are essential for ensuring that the installation complies with building codes and standards.
8. Waste Management: Proper disposal of waste materials generated during the installation process is another cost to consider. Efficient waste management practices can help control costs, but they still represent an additional expense.
In conclusion, the cost of installing MgO boards includes several components such as material costs, labor, tools and equipment, site preparation, finishing, transportation, permits, and waste management. While the initial investment may be higher than some traditional materials, the long-term benefits of MgO boards make them a worthwhile choice.
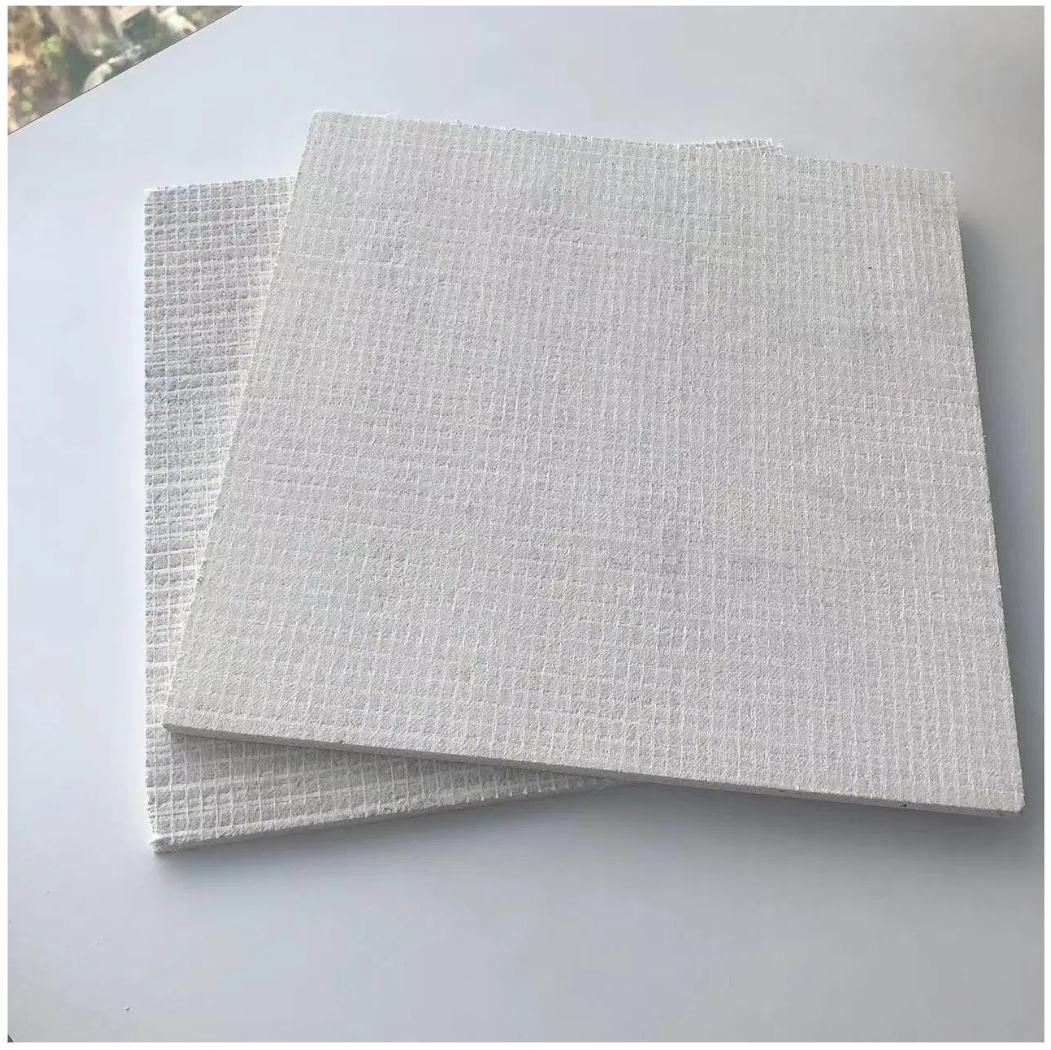
Post time: Jul-23-2024