Installing MgO panels involves several cost factors that can vary depending on the specifics of your project. Here’s a closer look at what influences the cost:
Quality and Type of MgO Panels: The cost of MgO panels can vary based on their quality and type. Higher-grade panels with enhanced features such as better fire resistance or improved moisture resistance will cost more. Additionally, specialized MgO panels for specific applications, such as exterior sheathing or flooring, can also influence the price.
Project Size and Scale: The overall size of your project plays a significant role in determining installation costs. Larger projects may benefit from bulk purchasing discounts on materials, but they also require more labor and longer installation times, which can increase total costs.
Site Conditions: The condition and location of the installation site can affect costs. For instance, if the site requires extensive preparation or is difficult to access, additional labor and equipment may be needed, increasing the overall cost.
Installation Complexity: Projects with complex designs or requiring intricate installation techniques will generally cost more. This includes buildings with curved walls, multiple angles, or specific structural requirements that demand precise cutting and fitting of MgO panels.
Local Labor Rates: Labor costs can vary significantly based on the geographic location of your project. Areas with higher living costs typically have higher labor rates, which can impact the overall cost of installing MgO panels.
Permits and Regulations: Depending on local building codes and regulations, obtaining the necessary permits for installing MgO panels can incur additional costs. Compliance with specific safety and building standards may also require extra materials or labor.
Finishing Requirements: The level of finishing required for your project can influence costs. High-end finishes, such as smooth walls for painting or surfaces prepared for tiling, require more detailed work and higher-quality finishing materials, adding to the overall expense.
Waste Management and Cleanup: Proper disposal of waste materials and site cleanup after installation is another factor to consider. Efficient waste management practices can help control costs, but they still represent an additional expense.
By considering these factors, you can better estimate the cost of installing MgO panels for your project. While the initial investment may be higher than some traditional materials, the durability, fire resistance, and long-term savings offered by MgO panels can make them a cost-effective choice in the long run.
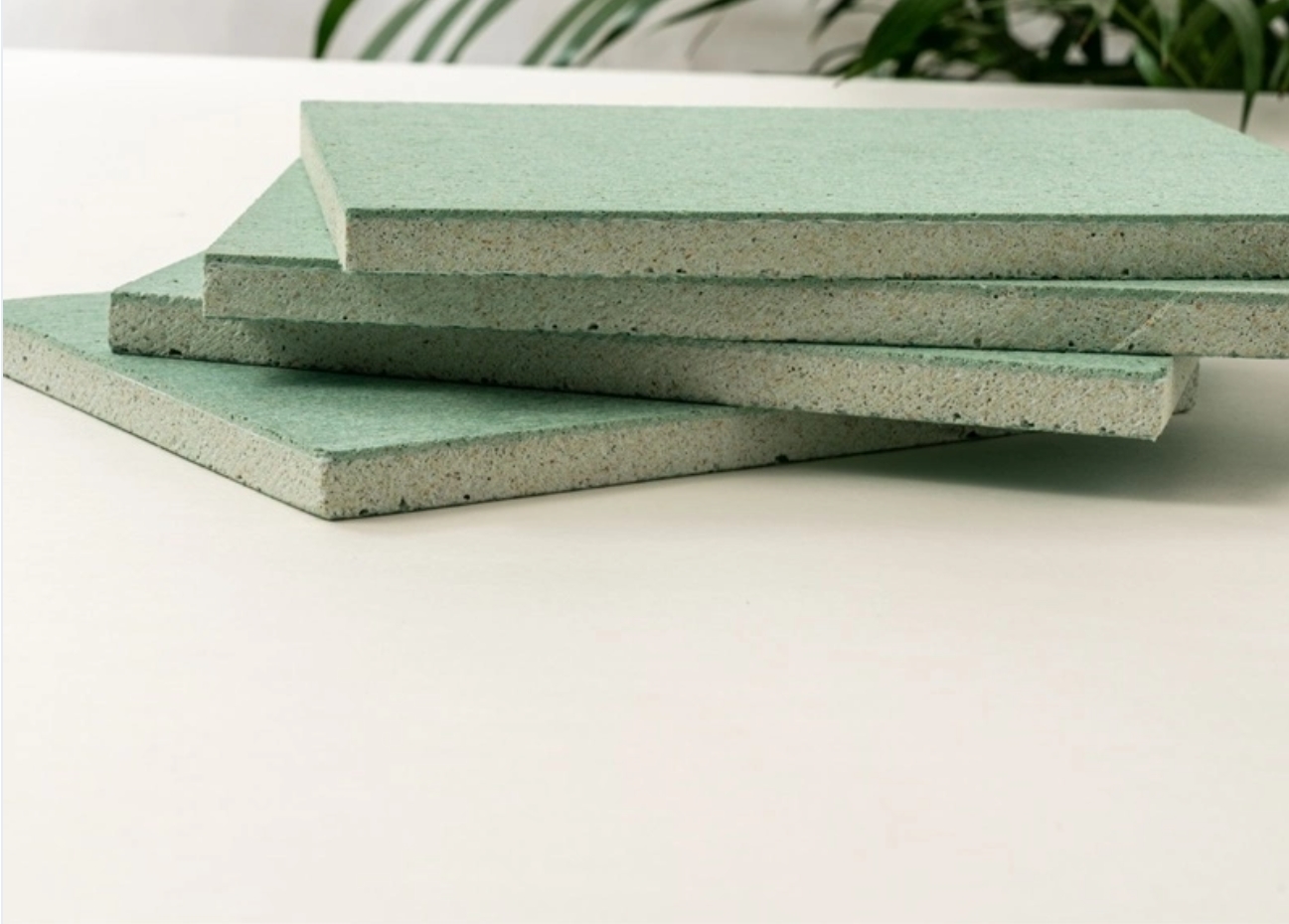
Post time: Jul-10-2024