To ensure that MgO panels last as long as the buildings they are used in, it is essential to focus on both production and installation processes. Here are detailed analyses and recommendations:
I. Key Measures in the Production Process
Selection of Raw Materials
1.High-Purity Magnesium Oxide: Ensure the use of high-purity magnesium oxide as the primary raw material. This will provide excellent physical and chemical properties, enhancing the durability of the panels.
2.High-Quality Additives: Choose high-quality fibers and fillers that meet standards to increase the toughness and strength of the panels, reducing the risk of cracking and deformation.
3.Magnesium Sulfate Additive Formula: Opt for MgO panels that use magnesium sulfate as an additive. This formula can further improve the strength and stability of the panels, reduce moisture absorption and efflorescence, and ensure excellent performance in various environments.
Optimization of the Production Process
1.Accurate Mixing Ratios: Strictly control the mixing ratios of magnesium oxide and additives to ensure uniform distribution and stability of the materials, producing consistently high-quality panels.
2.Even Mixing: Use efficient mixing equipment to ensure the materials are evenly mixed, reducing the occurrence of internal weak points.
3.Proper Curing: Conduct curing under appropriate temperature and time conditions to enhance the strength and stability of the panels. Insufficient curing can lead to inadequate strength and increase the likelihood of cracking.
Quality Control
1.Comprehensive Quality Testing: Perform thorough quality testing on each batch of MgO panels, including compressive strength, bending strength, fire resistance, and water resistance. Ensure that each panel meets quality standards before leaving the factory.
2.High-Standard Testing Equipment: Utilize advanced testing equipment and high-standard testing procedures to detect and address potential defects in production, ensuring the consistency of product quality.
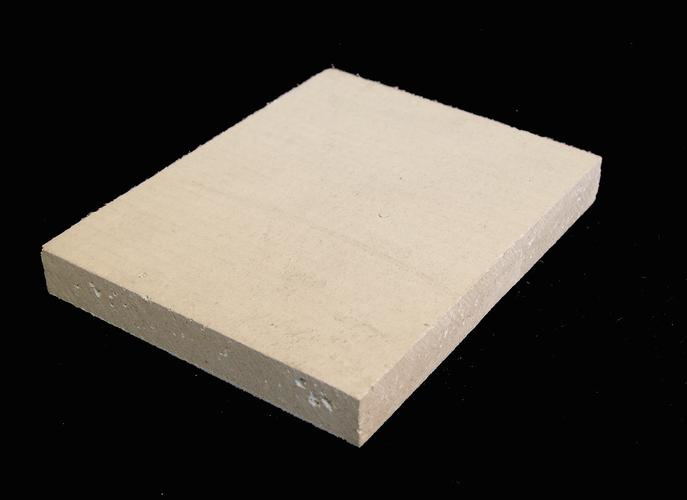
Post time: Jun-21-2024