With the arrival of the hot summer, MgO boards face high-temperature environments during the curing process. The workshop temperature can reach up to 45 degrees Celsius, while the ideal forming temperature for MgO is between 35 and 38 degrees Celsius. The most critical period is the several hours before demolding during the curing stage. If the temperature is too high during this time, moisture will evaporate too quickly, not allowing enough reaction time for the internal structure of the boards before the moisture is gone. This can result in unstable internal structures in the final boards, causing deformation and even cracks, which negatively impact the stability of the boards during later use.
To address this issue, we add certain additives to slow down the evaporation of moisture. Even under high temperatures, this ensures that there is sufficient reaction time for the internal materials of the boards during the moisture evaporation process. This prevents the negative impact of excessively high summer temperatures and rapid moisture evaporation on the internal structure of MgO boards.
The image below compares the different effects of various additives. If you have any other questions about MgO boards, please leave a comment or email us.
Managing High Temperatures During the Curing Process of MgO Boards in Summer With the arrival of the hot summer, MgO boards face high-temperature environments during the curing process. The workshop temperature can reach up to 45 degrees Celsius, while the ideal forming temperature for MgO is between 35 and 38 degrees Celsius. The most critical period is the several hours before demolding during the curing stage. If the temperature is too high during this time, moisture will evaporate too quickly, not allowing enough reaction time for the internal structure of the boards before the moisture is gone. This can result in unstable internal structures in the final boards, causing deformation and even crack
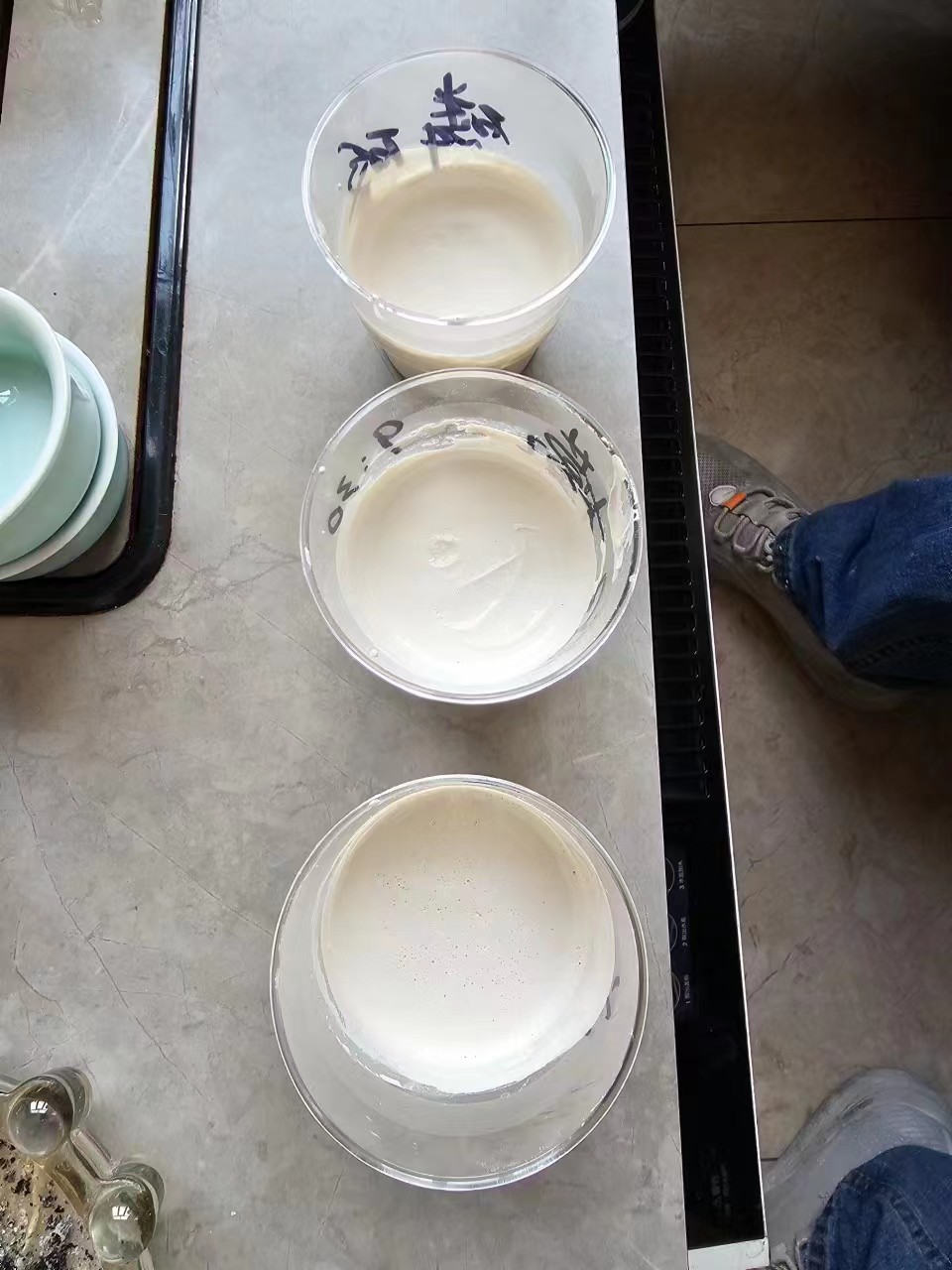
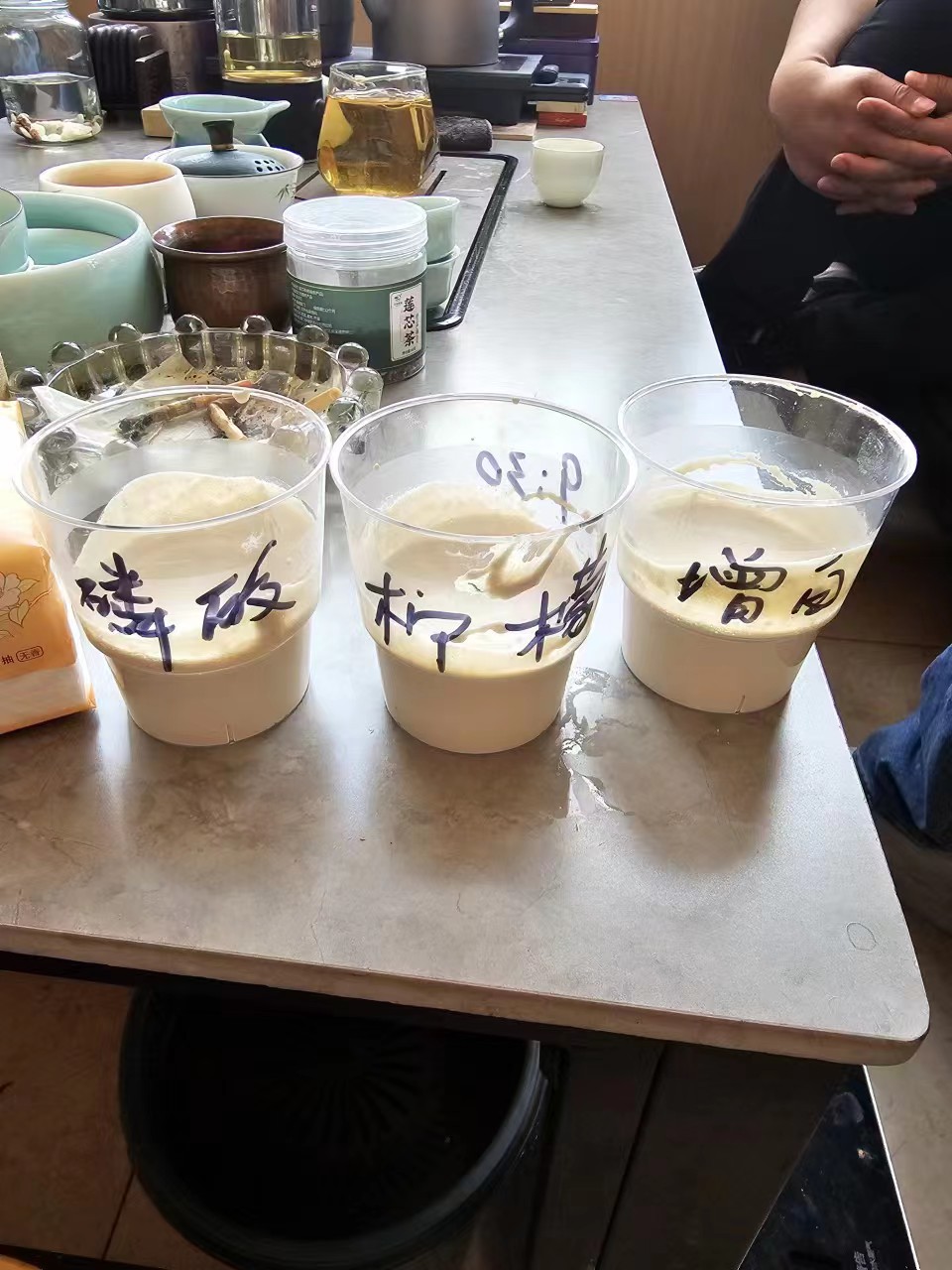
Post time: Jun-11-2024